As the global demand for beverages continues to grow, so does the need for efficient and innovative bottling solutions. In this article, we’ll explore the latest trends and advancements in industrial bottling equipment, highlighting key technologies and discussing their potential impact on the industry. Whether you’re a seasoned professional or new to the bottling world, this comprehensive overview will provide valuable insights into the future of this essential sector.
The Evolution of Bottling Machinery
The development of bottling equipment has come a long way since its inception, with manufacturers continually refining and enhancing their offerings to cater to changing market needs. Some key milestones include:
Automation: As with many industries, automation has become an integral part of bottling processes. Modern bottling lines incorporate sophisticated control systems, robotics, and vision technology to streamline operations and minimize human intervention. This not only enhances efficiency but also improves safety and product quality.
Flexibility: Today’s bottling machinery is designed with versatility in mind. Equipment can handle a wide range of container shapes and sizes, as well as accommodate different materials such as glass, plastic, and aluminum. This flexibility allows manufacturers to easily adapt to changing consumer preferences and regulations.
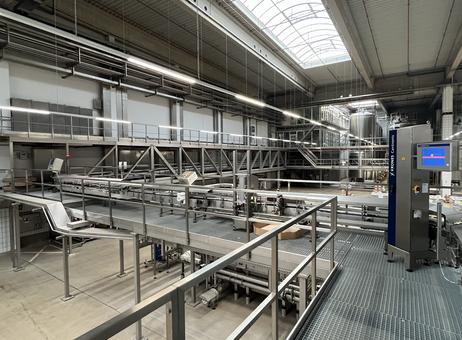
Cutting-Edge Technologies
Innovation continues to drive the bottling machinery sector forward. Let’s delve into some exciting technologies that are transforming the industry:
Digital Twins: This technology involves creating virtual replicas of physical systems, enabling operators to simulate and optimize production processes. Digital twins can help identify bottlenecks, predict equipment failures, and streamline maintenance activities, ultimately enhancing overall line efficiency.
Artificial Intelligence (AI) and Machine Learning: AI-powered tools can analyze vast amounts of data to optimize production schedules, predict equipment wear, and improve quality control. Machine learning algorithms can also adapt to changing conditions, enhancing equipment performance over time.
The Internet of Things (IoT): IoT-enabled devices collect and transmit real-time data from various points in the bottling process. This data can be used to monitor performance, identify inefficiencies, and facilitate remote maintenance, leading to significant cost savings and reduced downtime.
Sustainability and Eco-Friendly Solutions
Environmental considerations have become increasingly important in the bottling industry. Manufacturers are focusing on innovative solutions to minimize their ecological footprint:
Lightweight Containers: New materials and designs are being developed to reduce the weight of bottles and cans. This not only reduces the amount of raw materials needed but also cuts transportation costs and carbon emissions.
Energy-Efficient Equipment: Advances in motors, pumps, and compressors have led to significant energy savings. Additionally, innovative heat recovery and water reuse systems can further reduce a bottling plant’s environmental impact.
Biodegradable Packaging: Research into biodegradable materials, such as PLA (polylactic acid), is paving the way for more sustainable packaging solutions. These materials can break down naturally, reducing plastic waste and pollution.
The Role of Industry 4.0
Industry 4.0, or the Fourth Industrial Revolution, is transforming manufacturing processes across the globe. Its impact on bottling equipment includes:
Enhanced Connectivity: Industry 4.0 relies on seamless communication between machines, systems, and people. This interconnectedness allows for real-time monitoring, data sharing, and improved decision-making.
Big Data Analytics: The vast amounts of data generated by connected devices can be harnessed to optimize processes, predict equipment failures, and identify opportunities for improvement.
Customization: Advanced manufacturing techniques, such as 3D printing, enable the production of bespoke parts and components. This allows for greater equipment customization and faster development cycles.
The main manufacturers of bottling equipment
Krones AG: a global market leader from Germany in the design and manufacture of bottling and packaging equipment. They offer a wide range of solutions, including filling and capping machines, labeling systems, and complete bottling lines for various industries such as beverages, food, and pharmaceuticals.
Sidel : Sidel is a leading provider of equipment and services for the liquid packaging industry from France. Their extensive product portfolio includes blow molding machines for PET bottles, filling and capping machines, and complete packaging line solutions for beverages, food, and personal care products.
Tetra Pak: a multinational company specializing in food processing and packaging solutions. Originally from Switzerland, they are particularly known for their innovative aseptic packaging technology, which allows beverages and other liquid products to be stored without refrigeration for extended periods.
KHS GmbH: a prominent German manufacturer of filling and packaging systems for the beverage, food, and non-food industries. They offer a comprehensive range of equipment, including bottle washers, filling machines, labeling systems, and inspection technology.
Sacmi : Sacmi is an international group originally from Italy that focuses on providing complete solutions for the beverage, packaging, and ceramic industries. In the bottling sector, they offer solutions such as stretch blow molding machines, filling and capping systems, and labeling machines.
Pro Mach : Pro Mach is a leading provider of integrated packaging and processing products and solutions for various industries from the US. Their offerings include bottle filling and capping systems, labeling machines, and end-of-line equipment such as case packers and palletizers.
Focus on the SBO model from SIDEL
The SIDEL SBO series is a range of advanced stretch blow molding machines designed to produce high-quality PET (Polyethylene Terephthalate) bottles with optimal efficiency and minimal waste. These machines are known for their precision, speed, and flexibility, making them a popular choice among beverage manufacturers worldwide. In this article, we will explore the features, benefits, and applications of the SIDEL SBO series, providing a comprehensive overview of this innovative bottling technology.
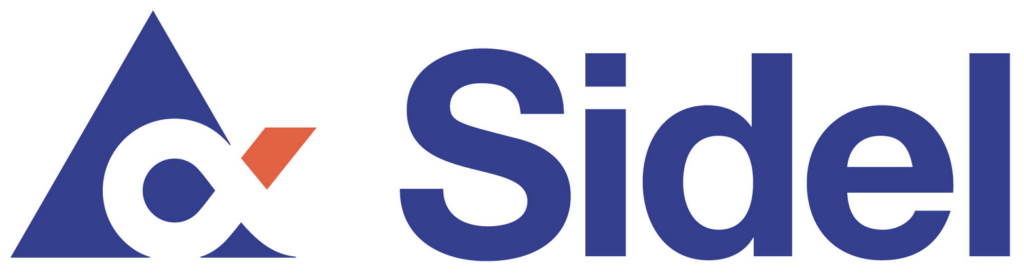
Key Features
The SIDEL SBO series incorporates numerous advanced features that set it apart from traditional stretch blow molding machines:
Modularity: The series offers a modular design, allowing manufacturers to configure the machine according to their specific production needs. This modularity enables easy adaptation to different bottle shapes, sizes, and production volumes, ensuring maximum versatility.
High Output Rates: Thanks to its efficient design and advanced technology, the series can achieve impressive output rates. Depending on the specific model and configuration, these machines can produce up to 2,300 bottles per hour, per mold.
Energy Efficiency: The series is designed with energy-saving features, such as electrically-driven stretch rods and optimized oven configurations. These innovations can result in energy savings of up to 45% compared to traditional blow molding machines.
Quick Changeovers: The series is equipped with user-friendly features that facilitate rapid format changeovers. This allows manufacturers to easily switch between different bottle sizes and shapes, minimizing downtime and maximizing production efficiency.
An example of SIDEL SBO 18 from 2004 on sale
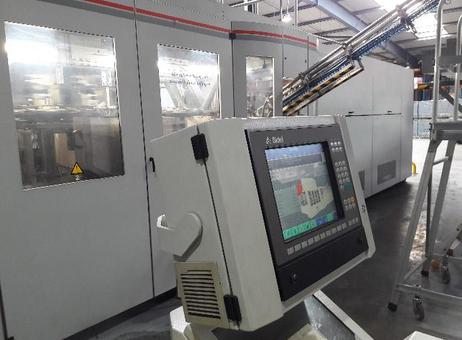
Benefits of the SBO Series
Enhanced Product Quality: The precise control and optimized preform heating system of the SBO series ensure consistent, high-quality bottle production. This translates to improved product appearance and performance, ultimately resulting in greater consumer satisfaction.
Reduced Waste: The SBO series’ advanced technology minimizes waste by reducing scrap rates and maximizing the use of raw materials. This not only lowers production costs but also contributes to a more sustainable operation.
Flexibility: The modular design of the SBO series allows manufacturers to adapt their production lines to changing market demands quickly. This flexibility enables them to respond to new trends and opportunities more effectively.
Lower Total Cost of Ownership: The energy efficiency, reduced waste, and minimal maintenance requirements of the SBO series can result in significant cost savings over the machine’s lifetime.
An example of SIDEL SBO 10 series 2 from 2003 on sale in Germany
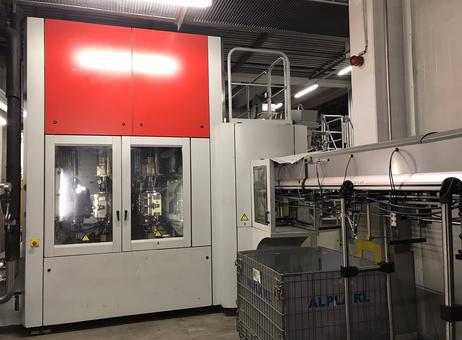
Applications
The SBO series is suitable for a wide range of applications within the beverage industry, including:
Carbonated Soft Drinks (CSD): can produce PET bottles for carbonated beverages with excellent performance characteristics, such as high pressure resistance and consistent barrier properties.
Water: is ideal for producing PET bottles for still and sparkling water, ensuring optimal product quality and shelf life.
Juice and Tea: can accommodate various bottle designs and sizes, making it a suitable choice for juice and tea packaging.
Dairy and Liquid Dairy Products: can produce PET bottles for dairy products, such as flavored milk and drinkable yogurt, providing an attractive and functional packaging solution.
Some examples of offers you can find on Exapro
- Krones 20,000 bph Beer or carbonated drinks bottling line from 2004
- Krones Craftmate Cans filling line from 2020
- LMF EcoPET 2200-B Compresso from 2004 based in Austria
- Sraml I12P12PT Line for non-returnable glass bottles from 2022 in the Netherlands
- GEA AromaPlus dealcoholization machine from 2021 in Germany
- Haloila Octopus T-200 Stretch wrapping machine