In the realm of industrial manufacturing, laser and waterjet cutting machines stand out for their precision, versatility, and efficiency. However, the secret to sustaining these attributes over time lies in diligent maintenance. Neglecting this crucial aspect can lead to decreased performance, higher operational costs, and reduced machine lifespan. This guide aims to equip you with a thorough understanding of maintaining your laser and waterjet machines, ensuring they continue to operate at their peak.
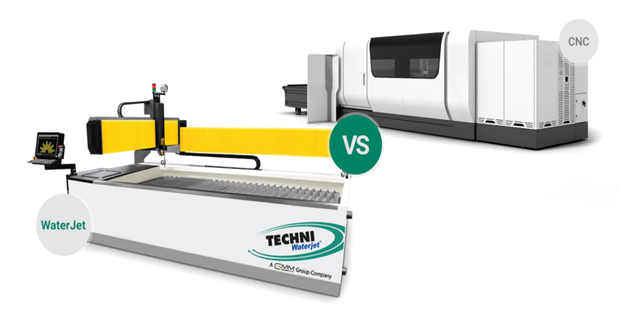
Understanding Laser and Waterjet Cutting Technologies
Laser and waterjet cutting are two of the most advanced manufacturing technologies available today. While laser cutting uses a high-powered laser beam focused through optics to melt, burn, or vaporize material, waterjet cutting employs a high-pressure stream of water, sometimes mixed with an abrasive substance, to cut through materials.
- Comparison Chart
- Laser Cutting: High precision, suitable for metal and non-metal, high speed, thermal process.
- Waterjet Cutting: Versatile on all materials, no heat-affected zone, slower than laser, mechanical process.
Understanding these technologies’ fundamental principles is crucial for appreciating the maintenance they require.
Why Regular Maintenance is Crucial for Laser and Waterjet Machines?
Regular maintenance is the cornerstone of operational efficiency and product quality. For instance, a well-maintained laser cutter ensures consistent cutting power and precision, while a properly serviced waterjet cutting machine preserves the integrity of its cutting stream, minimizing wear and tear on the system.
What Are the Common Maintenance Needs for Laser Cutting Machines?
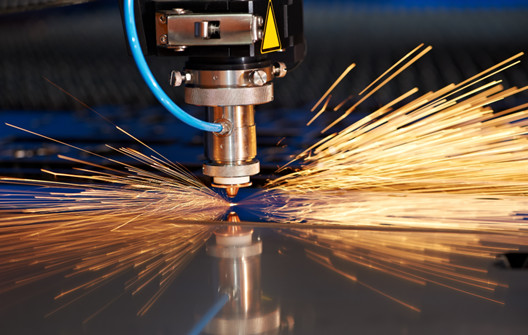
Maintaining a laser cutting machine involves a series of regular tasks to ensure its optimal performance.
- Regular Maintenance Tasks
- Lens cleaning and inspection
- Alignment of mirrors
- Laser source maintenance
- Checking and cleaning the cooling system
How Often Should You Clean a Laser Cutter?
The frequency of cleaning a laser cutter depends on its usage intensity. However, a general guideline is to inspect and clean crucial components, such as the lens and mirrors, weekly.
What Are the Key Components to Check During Laser Cutter Maintenance?
Ensuring the laser cutter’s efficiency involves paying close attention to:
- The laser source for signs of wear or degradation
- Mirrors and lenses for cleanliness and proper alignment
- The cooling system to prevent overheating
How to Maintain the Laser Source for Optimal Performance?
The laser source is the heart of the laser-cutting machine. Regular checks for output efficiency, along with adherence to the manufacturer’s maintenance schedule, are imperative.
The Importance of Mirror Alignment and Cleaning
Misaligned or dirty mirrors can significantly affect the machine’s cutting accuracy and efficiency. A step-by-step guide includes inspecting for dirt or damage, cleaning with a recommended solvent, and aligning as per the manufacturer’s instructions.
Cooling System Maintenance for Laser Cutters
The cooling system plays a crucial role in maintaining optimal operating temperatures. Regular flushing, checking for leaks, and ensuring the coolant’s quality are essential steps.
What Are the Common Maintenance Needs for Waterjet Cutting Machines?
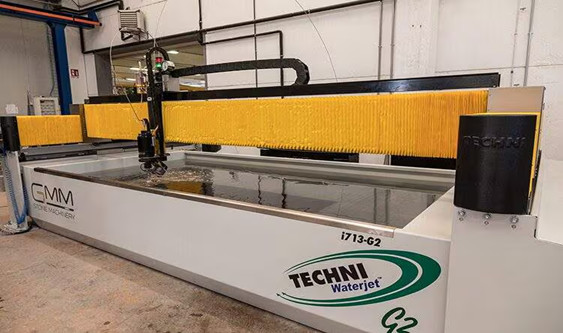
Similar to laser cutters, waterjet machines also have specific maintenance requirements to ensure their performance and longevity.
- Regular Maintenance Tasks
- Inspecting and replacing worn nozzles
- Monitoring water quality and filtration systems
- Cleaning the catcher tank to prevent buildup
The Significance of Water Quality in Waterjet Maintenance
Water quality directly impacts the cutting performance and lifespan of the pump and nozzles. Regular testing and treatment can prevent issues related to sediment or chemical imbalance.
Abrasive and Nozzle Wear: Maintenance and Replacement
The abrasive and nozzle are critical to the waterjet’s cutting precision. Monitoring for wear and timely replacement is crucial to maintaining cutting accuracy.
Keeping the Catcher Tank Clean: Why and How?
The catcher tank collects the spent water and abrasive after cutting. Regular cleaning prevents buildup that can affect machine performance.
How to Troubleshoot Common Issues in Laser and Waterjet Machines?
Identifying and addressing common issues promptly can prevent downtime and costly repairs.
- Common Issues and Troubleshooting Tips
- Reduced cutting power or accuracy
- Inconsistent cut quality
- Overheating of components
Dealing with Reduced Cutting Power in Laser Machines
Factors such as a dirty lens, misaligned mirrors, or a failing laser source can reduce cutting power. Systematic checks can help identify and rectify these issues.
Addressing Inconsistent Cut Quality in Waterjet Machines
Inconsistent cut quality in waterjet machines often results from worn nozzles, poor water quality, or issues with the abrasive feed. Regular maintenance checks and adjustments can significantly improve performance.
Implementing a Preventative Maintenance Schedule
A preventative maintenance schedule is not just a recommendation; it’s a necessity for ensuring the longevity and efficiency of your laser and waterjet cutting machines. By proactively addressing potential issues, you can avoid unexpected downtime and expensive repairs.
What Should Be Included in a Laser Cutter Maintenance Schedule?
A comprehensive maintenance schedule for a laser cutter should include:
- Daily checks of the cooling system and laser output
- Weekly cleaning of lenses and mirrors
- Monthly inspections of the laser source and alignment of optics
What Should Be Included in a Waterjet Cutter Maintenance Schedule?
For waterjet cutters, a maintenance schedule should focus on:
- Daily inspections of water and abrasive levels
- Weekly checks of nozzles and pumps for wear
- Monthly cleaning of the catcher tank and filtration system
Training and Documentation for Maintenance Procedures
Equipping your team with the necessary training on maintenance procedures is crucial for the effective upkeep of your machinery. Additionally, maintaining detailed records of maintenance activities, issues encountered, and solutions implemented can serve as a valuable reference over the lifespan of your machines.
Enhancing Machine Lifespan and Efficiency Through Upgrades
Over time, advances in technology may offer opportunities to enhance the performance of your laser and waterjet machines through upgrades. Whether it’s upgrading the laser source for higher efficiency or incorporating a more advanced abrasive delivery system for your waterjet cutter, staying abreast of technological improvements can provide significant benefits.
Conclusion: The Impact of Maintenance on Machine Performance
The maintenance of laser and waterjet cutting machines is a crucial aspect that directly impacts their performance, efficiency, and longevity. By understanding the specific needs of these machines and implementing a structured maintenance schedule, you can ensure they continue to operate at their best. Remember, the effort and resources invested in maintenance are minor compared to the costs associated with downtime and machine replacement. Therefore, make maintenance a priority to maximize the return on your investment in these cutting-edge technologies.